ISO 9001 Standard Manufacturing Procedure
In the world of manufacturing, maintaining consistently high-quality products is paramount. Achieving this level of quality requires well-defined processes, meticulous attention to detail, and a commitment to continuous improvement. One of the most widely recognized tools for achieving and demonstrating quality management in manufacturing is ISO 9001. This blog post will explore ISO 9001's significance in the manufacturing sector, its key components, and how it helps organizations streamline their manufacturing procedures for optimal results.
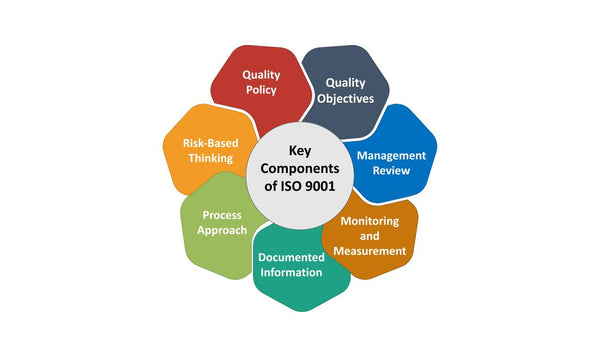
Understanding ISO 9001 Standard Manufacturing: The Basics
ISO 9001 is an international standard developed by the International Organization for Standardization (ISO). It sets out the criteria for a quality management system (QMS) and applies to organizations of all sizes and industries. The standard provides a framework for organizations to establish and maintain processes that ensure the consistent delivery of high-quality products and services while meeting customer and regulatory requirements.
Key Components Of ISO 9001 Standard Manufacturing
ISO 9001 is structured around several key components, each of which plays a vital role in shaping a robust quality management system:
- Quality Policy: Organizations must define a clear quality policy that aligns with their strategic objectives. The policy should reflect the organization's commitment to meeting customer needs and continuously improving its processes.
- Quality Objectives: Establishing measurable quality objectives helps organizations work toward specific, quantifiable goals. These objectives should be aligned with the quality policy and consistent with the organization's mission.
- Risk-Based Thinking: ISO 9001 emphasizes a proactive approach to risk management. Organizations must identify and assess risks and opportunities that could affect their ability to deliver products that meet customer requirements.
- Process Approach: The standard encourages a process-oriented approach to quality management. Organizations should identify and define the processes necessary to deliver conforming products and continuously monitor and improve them.
- Documented Information: ISO 9001 emphasizes the importance of documenting information related to the QMS, including processes, procedures, and records. This documentation provides a clear framework for how activities are performed.
- Monitoring and Measurement: Organizations must establish processes for monitoring and measuring performance. This includes customer satisfaction, process performance, product conformity, and more.
- Management Review: Top management reviews the organization's QMS at planned intervals to ensure its suitability, adequacy, effectiveness, and alignment with strategic objectives.
Significance Of ISO 9001 Standard Manufacturing
ISO 9001 holds particular significance in the manufacturing sector for several reasons:
- Consistency: Manufacturing involves numerous processes and complex supply chains. ISO 9001 helps organizations standardize these processes, ensuring products meet consistent quality standards.
- Customer Satisfaction: Manufacturing companies often have diverse customer bases. ISO 9001 helps organizations understand and meet customer needs and expectations, increasing satisfaction and loyalty.
- Regulatory Compliance: Manufacturing is subject to numerous regulations and quality standards. ISO 9001 can assist organizations in demonstrating compliance with these requirements.
- Operational Efficiency: ISO 9001 encourages a process-based approach, leading to improved efficiency, reduced waste, and cost savings.
- Competitive Advantage: ISO 9001 certification can be a competitive differentiator in the manufacturing industry, as it demonstrates a commitment to quality that can attract customers and business partners.
- Continuous Improvement: The standard's focus on continuous improvement aligns with the manufacturing sector's innovation and process optimization drive.
Implementing ISO 9001 Standard Manufacturing
Implementing ISO 9001 in a manufacturing environment involves several key steps:
- Leadership Commitment: Top management must demonstrate their commitment to ISO 9001 and provide the necessary resources for implementation.
- Gap Analysis: Conduct a thorough assessment of existing quality management practices to identify gaps that need to be addressed to meet ISO 9001 requirements.
- Quality Policy: Develop a quality policy that reflects the organization's commitment to quality and aligns with its strategic objectives.
- Process Mapping: Identify and define key manufacturing processes, including inputs, outputs, and the sequence of activities.
- Documentation: Create and maintain documentation of processes, procedures, work instructions, and records to ensure consistency and compliance with ISO 9001 requirements.
- Training and Awareness: Train employees to understand their roles and responsibilities in maintaining the QMS.
- Internal Audits: Conduct regular internal audits to assess the QMS's effectiveness and identify improvement opportunities.
- Management Review: Hold management reviews to evaluate the performance of the QMS and make informed decisions about its ongoing suitability and effectiveness.
- Corrective and Preventive Actions: Implement corrective and preventive actions to address nonconformities and continually improve the QMS.
Benefits Of ISO 9001 Standard Manufacturing
Manufacturing organizations that implement ISO 9001 stand to gain numerous benefits:
- Enhanced Product Quality: ISO 9001 helps organizations deliver consistently high-quality products, reducing defects and customer complaints.
- Increased Efficiency: Process optimization and waste reduction improve operational efficiency and cost savings.
- Market Access: ISO 9001 certification can open doors to new markets and customers prioritizing quality and reliability.
- Better Risk Management: Focusing on risk-based thinking allows organizations to identify and mitigate potential risks before they become issues.
- Improved Supplier Relationships: Organizations can extend ISO 9001 principles to their supply chain, fostering better supplier relationships and ensuring the quality of raw materials and components.
- Competitive Advantage: ISO 9001 certification can set organizations apart from competitors, especially in industries where quality is a key differentiator.
- Customer Satisfaction: Meeting or exceeding customer expectations increases customer satisfaction and loyalty.
Challenges Of Implementing ISO 9001 In Manufacturing
While ISO 9001 offers substantial benefits, implementation can pose challenges, including:
- Resource Investment: Implementing and maintaining a QMS requires time, personnel, and financial resources.
- Cultural Change: Shifting organizational culture to prioritize quality and continuous improvement can be met with resistance from employees accustomed to existing practices.
- Documentation: Maintaining extensive documentation can be labor-intensive, requiring ongoing effort.
- Complexity: ISO 9001 requirements can be complex and may necessitate expertise in quality management systems.
Conclusion
ISO 9001 is a valuable tool for manufacturing organizations seeking to enhance product quality, customer satisfaction, and operational efficiency. By providing a structured framework for quality management, ISO 9001 enables organizations to deliver high-quality products while meeting customer and regulatory requirements consistently. While implementing ISO 9001 may present challenges, the long-term benefits make it worthwhile for any manufacturing company looking to excel in today's competitive market. Ultimately, ISO 9001 stands as a testament to an organization's commitment to quality and customer satisfaction, helping them thrive in the manufacturing industry.